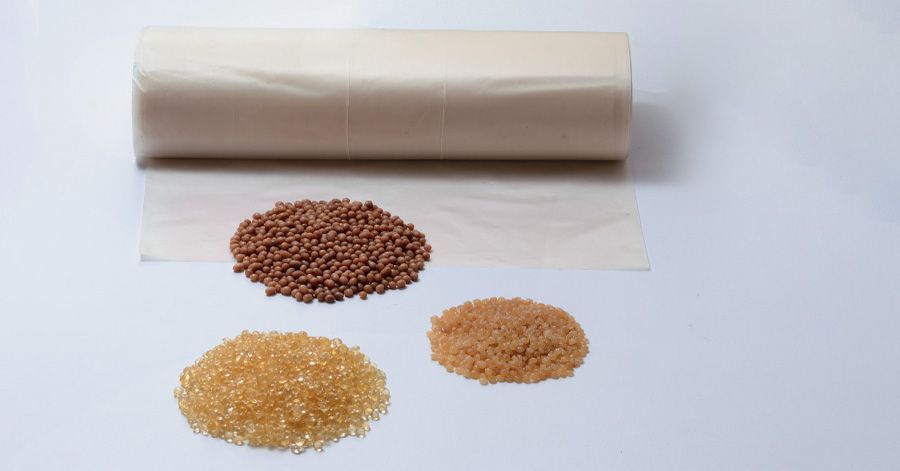
INNOVATION EXTRUDER
Intype Enterprise has built up 59 years of experience in producing extruders, though the firm is placing greater consideration on rapidly degrading of the global environment. In the past 20 years, Intype has become an active contributor to building up a global ecosystem, enabling them to reuse the products manufactured by their own extruders and avoid further waste. The firm thus has revolved its operations around three key design principles: environmentally friendly manufacturing, sustainability and circular economy.
BIODEGRADABLE PELLETIZING. FILM
The firm has continued to work with technologies based in Taiwan, Japan and the U.S. in producing biodegradable pelletizing and blown film extruders. The high-performing plant-based bioplastic that Intype machine produces has massively cut the reliance on using petro based resins, thus improving the end-product physical properties, and cutting CO2 emissions. Such a technology has enabled Intype to improve the economy and performance of recyclable materials, and further allowing this compostable end product safely become biodegradable in nature.
CONTINUOUS BEAD FOAMING
The next product that Intype offers is the “continuous bead foaming extruder,” which has replaced the traditional model of batch production, and cutting down production costs as well. Poly foam processing not only cuts down weight, but also the usage of plastics. Applying this technology in public transportation can reduce gas usage, or in the case for construction materials, improve thermal insulation and reduce energy consumption. With the risk of an intensifying greenhouse effect in the future, the carbon-reducing traits of foaming technology could mean a huge breakthrough for lifestyles if it is successfully applied to sports equipment and bionics.
WOOD-IMITATION POLYMER
Intype has also rolled out a new environmentally-friendly compound material that was developed in-house: wood-imitation polymer and irregular-shape extruding machines. This combination allows the firm to offer end products that appear incredibly similar to the real thing, including the texture, wood pattern, and weight. The firm has not added any wood flour, non-toxic materials, and has made the end product water resistant. In consideration of client needs, the wood-imitation polymer is also malleable for further processing, making it a convenient choice for fast manufacturing, and ticks the box for recyclable use. What's more, the wood-imitation polymer removes the need for actual wood cutting and the lengthy process of processing real wood.
The strength of nature, especially when it fights back, so it's really up to us to make the environment an absolute priority. Intype thus considers it prudent to make strategic decisions, join us!
- Related Products
- Applications
Digital control of components and actual monitoring of production processes and quality, which also means that we are always close to the needs of customers.
INNOVATION EXTRUDER | Plastic Profile Extrusion Solutions | Intype
Located in Taiwan since 1963, Intype Enterprise Co., Ltd. is a high efficiency plastic extrusion machines manufacturer. Their main plastic extrusion machines include, sustainable plastic extrusions, continuous bead foam machines, supercritical reaction pelletizers, medical tube extrusion lines and profile extrusion machinery. Their offerings also encompass medical tube extrusion lines and profile extrusion systems. Intype is committed to innovation, quality, and environmental sustainability, focusing on efficient, eco-friendly technologies.
Discover Intype's advanced Plastic Extrusion Machines, a blend of innovation and 60 years of expertise. Specializing in TPE Wood-like Profiles, Continuous Bead Foam, and Supercritical Reaction Pelletizing, our machines are designed for efficiency and sustainability. Ideal for B2B buyers in the plastic extrusion industry, our products range from Medical Tube Extrusion Lines to Profile Extrusion and Recycling Solutions. Intype machines are synonymous with quality, precision, and eco-friendliness, ensuring optimal performance and environmental responsibility. Join the forefront of plastic extrusion technology with Intype's reliable and advanced solutions.
Intype has been providing customers with high efficiency plastic extrusion machines since 1963, with both advanced technology and 50 years of experience, Intype ensures that each customer's requirements are met.